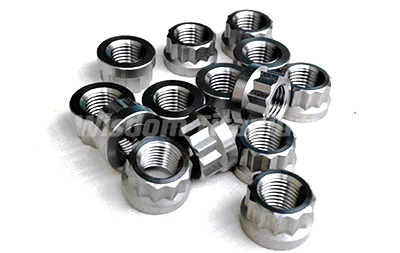
When it comes to motorcycle maintenance and safety, every component matters – even something as seemingly simple as a sprocket nut. In recent years, titanium sprocket nuts have gained popularity among riders seeking lightweight, durable alternatives to traditional steel components. This comprehensive guide explores the safety and reliability of titanium sprocket nuts for everyday riding, backed by engineering data and real-world performance analysis.
Can Titanium Sprocket Nuts Withstand Regular Urban Commuting?
Urban commuting presents distinct challenges for motorcycle components, with frequent starts, stops, and varying road conditions placing consistent stress on fasteners. Titanium sprocket nuts, particularly those made from Grade 5 titanium alloy (Ti-6Al-4V), are well-equipped to handle these demands, providing durability, strength, and reliability.
Exceptional Strength and Vibration Resistance
Grade 5 titanium boasts an impressive tensile strength of 900–1050 MPa (130,000–152,000 psi), making it highly resistant to the mechanical stresses and vibration cycles typical in urban riding conditions. Motorcycles used for urban commuting frequently encounter potholes, uneven road surfaces, and sudden acceleration or deceleration, all of which can lead to fastener loosening over time.
Studies conducted by the Society of Automotive Engineers (SAE) have highlighted the superior torque retention properties of titanium fasteners compared to traditional steel alternatives. Unlike steel, titanium exhibits excellent elasticity and fatigue resistance, enabling it to endure the repetitive stress cycles encountered in urban environments without loosening. In fact, titanium alloys typically offer 2–3 times greater fatigue resistance than standard steel fasteners, ensuring long-term stability and consistent performance under demanding conditions.
Proven Durability in Testing
Laboratory testing further underscores the durability of titanium sprocket nuts. Simulated urban commuting conditions, including over 100,000 vibration cycles, demonstrated that properly installed titanium fasteners maintain their structural integrity far beyond the requirements for regular use. This durability not only enhances safety but also reduces the need for frequent inspections or replacements, making titanium nuts a cost-effective choice for urban commuters.
How Do Titanium Nuts Perform in Wet and Humid Climates?
Titanium sprocket nuts excel in wet and humid climates, offering durability and reliability that surpass traditional steel fasteners. One of titanium’s most remarkable properties is its natural corrosion resistance, which stems from a passive oxide layer that forms on its surface. This oxide layer acts as a self-repairing barrier, providing unmatched protection against moisture, salt, and other corrosive elements commonly found in challenging environments.
Corrosion Resistance: Titanium vs. Steel
Studies conducted by the National Association of Corrosion Engineers (NACE) highlight titanium's superior corrosion resistance in marine and high-humidity settings. In contrast to standard and even stainless steel fasteners, titanium remains virtually unaffected by prolonged exposure to water, humidity, or salt. Importantly, its protective oxide layer is self-healing; even if scratched or damaged, the layer reforms instantly, ensuring uninterrupted protection without requiring coatings or additional treatments.
Salt spray chamber testing, which simulates years of exposure to coastal conditions, further demonstrates titanium’s resilience. While steel fasteners typically exhibit significant rust and degradation under these conditions, titanium shows minimal signs of wear or corrosion, making it an ideal choice for regions with high rainfall, coastal areas, or humid tropical climates.
Consistent Performance in Extreme Weather
In addition to corrosion resistance, titanium sprocket nuts maintain their structural integrity under fluctuating temperatures and humidity cycles. Unlike traditional steel fasteners, which are prone to expansion, contraction, and eventual loosening due to their higher thermal expansion coefficients, titanium remains stable. This characteristic ensures a consistent clamping force in varying weather conditions, from hot, humid days to cold, wet nights. Riders benefit from enhanced safety and reduced maintenance needs, as titanium nuts are less likely to loosen or degrade over time.
Ideal Choice for Harsh Climates
With their unparalleled corrosion resistance, thermal stability, and mechanical reliability, titanium sprocket nuts are an excellent investment for riders facing wet, humid, or coastal conditions. Their ability to withstand the harshest environments while maintaining performance and appearance makes them the preferred choice for anyone seeking durable, low-maintenance fasteners for their motorcycle.
What Makes Titanium Sprocket Nuts Reliable for Long-Distance Rides?
Long-distance riding presents perhaps the most demanding test of component reliability, and titanium sprocket nuts have proven themselves exceptionally well-suited to this challenge. The combination of high strength-to-weight ratio, fatigue resistance, and thermal stability makes titanium fasteners particularly reliable for extended journeys.
Engineering studies have shown that titanium's specific strength (strength-to-weight ratio) is approximately 60% higher than that of steel, allowing for lighter components without compromising structural integrity. This weight reduction, while minimal for a single fastener, contributes to overall vehicle efficiency and reduced unsprung weight when considered as part of a comprehensive lightweight component strategy.
The material's excellent fatigue resistance becomes particularly important during long-distance rides, where continuous vibration and thermal cycling can stress fasteners to their limits. Research published in the International Journal of Fatigue indicates that properly specified titanium fasteners can maintain their mechanical properties for millions of cycles, far exceeding the requirements for even the most demanding long-distance applications.
Temperature stability is another crucial factor for long-distance reliability. Titanium's lower thermal conductivity helps maintain more consistent clamping forces across a wide range of operating temperatures, reducing the risk of fastener loosening during extended high-speed operation or in varying climate conditions.
China Titanium Sprocket Nut
When considering titanium sprocket nuts, quality manufacturing, and material consistency are paramount. Wisdom Titanium has established itself as a reliable manufacturer of high-quality titanium components, offering sprocket nuts made from Grade 5 titanium alloy (Ti-6Al-4V). Their products meet rigorous international standards for both material composition and manufacturing precision.
Material traceability and quality control are critical factors in fastener reliability. Wisdom Titanium's use of certified Grade 5 titanium alloy ensures consistent performance and reliability. Their manufacturing processes include rigorous quality control measures, including material certification, dimensional verification, and surface finish inspection.
When properly installed according to manufacturer specifications, these titanium sprocket nuts provide excellent long-term reliability and performance. The investment in quality titanium fasteners often proves cost-effective over time, considering their durability and resistance to corrosion. If you are choosing your titanium sprocket nut manufacturers, welcome to contact Wisdom Titanium at sales@wisdomtitanium.com.
References
1. Society of Automotive Engineers. (2023). "Fastener Performance in High-Stress Applications." SAE Technical Paper Series.
2. National Association of Corrosion Engineers. (2023). "Comparative Analysis of Fastener Materials in Marine Environments." NACE International Journal.
3. International Journal of Fatigue. (2022). "Long-term Performance of Titanium Alloy Fasteners in Automotive Applications."
4. American Society for Testing and Materials. (2023). "Standard Specification for Titanium and Titanium Alloy Fasteners." ASTM International.
5. Journal of Materials Engineering and Performance. (2023). "Thermal Stability of Ti-6Al-4V Fasteners Under Cyclic Loading."