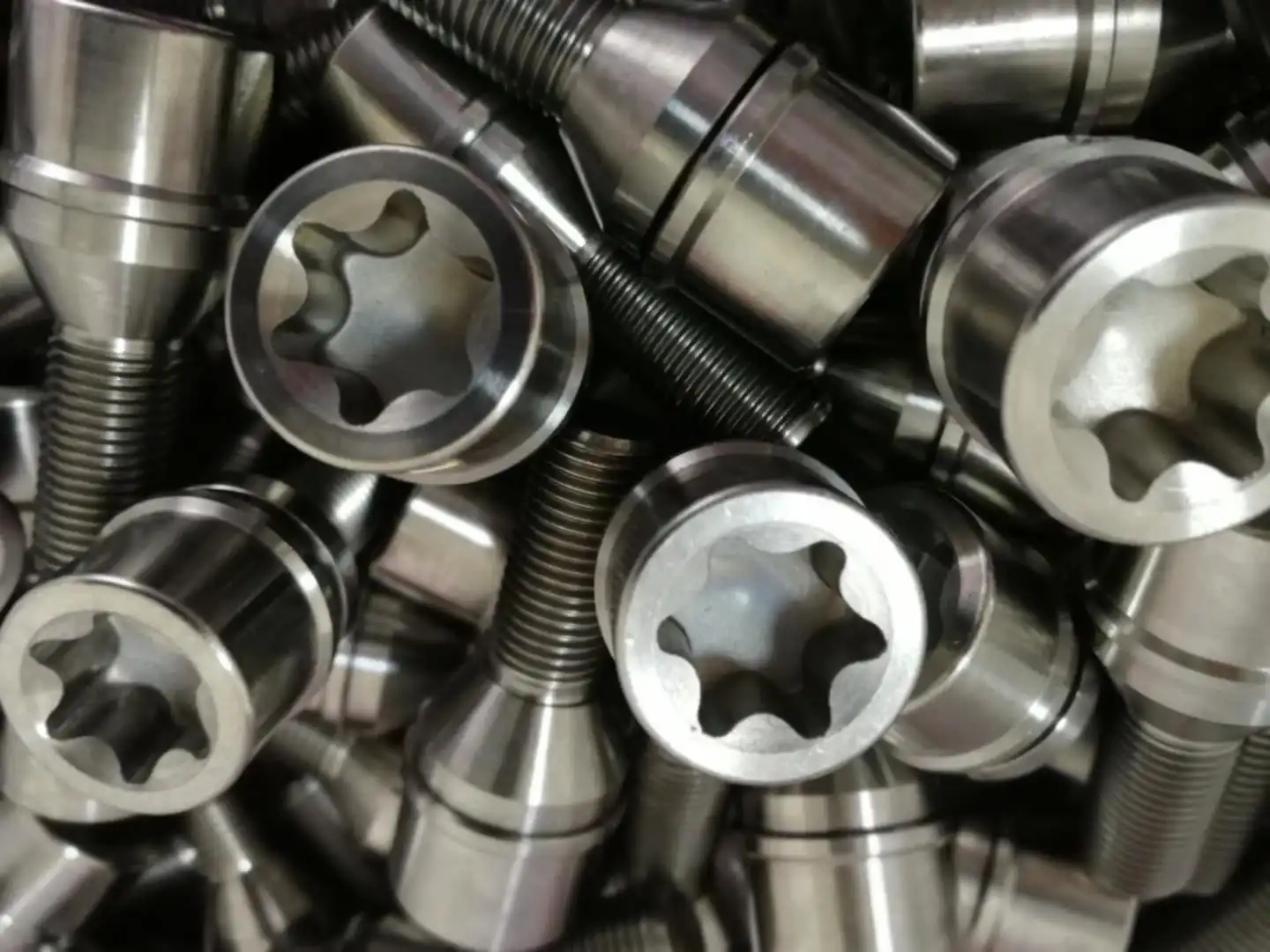
Introduction
In the world of automotive engineering and high-performance vehicles, the choice of fasteners can significantly impact a vehicle's performance, safety, and longevity. Two types of bolts that often come under comparison are titanium lug bolts and Grade 8 steel bolts. Both are known for their high strength and are used in critical applications where failure is not an option.
Titanium alloy lug bolts have gained popularity in recent years, particularly in racing and high-performance automotive applications. They are prized for their exceptional strength-to-weight ratio, corrosion resistance, and durability. On the other hand, Grade 8 bolts have long been the industry standard for high-strength fasteners in various applications, including automotive, construction, and heavy machinery.
The question of whether titanium lug bolts are stronger than Grade 8 bolts is not as straightforward as it might seem. Strength in fasteners is a multifaceted concept that involves various factors beyond just tensile strength. To answer this question comprehensively, we need to delve into the material properties of both types of bolts, analyze their strengths in different contexts, and consider other factors that contribute to their overall performance and suitability for specific applications.
Material Property Comparison
Titanium alloy lug bolts, typically made from Ti-6Al-4V (Grade 5 titanium), offer a unique set of physical properties that make them attractive for high-performance applications. The key characteristics of titanium alloy lug bolts include:
1. High strength-to-weight ratio: Titanium alloys have a density of about 4.51 g/cm³, roughly 40% less than steel, while maintaining comparable strength.
2. Excellent corrosion resistance: Titanium forms a stable oxide layer on its surface, providing superior resistance to various corrosive environments.
3. High fatigue strength: Titanium alloys exhibit excellent resistance to cyclic loading, crucial for components subjected to repeated stress.
4. Low thermal expansion: Titanium has a lower coefficient of thermal expansion compared to steel, which can be advantageous in applications with wide temperature variations.
Grade 8 bolts, made from medium carbon alloy steel, are known for their high strength and durability. Their key properties include:
1. High tensile strength: Grade 8 bolts typically have a minimum tensile strength of 150,000 psi (1034 MPa).
2. Good ductility: Despite their high strength, Grade 8 bolts maintain sufficient ductility to prevent brittle failure.
3. Resistance to fatigue: While not as high as titanium, Grade 8 bolts offer good resistance to cyclic loading.
4. Cost-effectiveness: Grade 8 bolts are generally more affordable than titanium alternatives, making them suitable for a wide range of applications.
Strength Analysis
When comparing the strength of titanium lug bolts to Grade 8 bolts, it's essential to consider various aspects of strength, including tensile strength, yield strength, and proof load.
Grade 8 bolts are known for their high tensile strength, with a minimum requirement of 150,000 psi (1034 MPa). The yield strength of Grade 8 bolts is typically around 130,000 psi (896 MPa), and they have a proof load of about 120,000 psi (827 MPa). These values make Grade 8 bolts suitable for a wide range of high-stress applications.
Titanium alloy lug bolts, specifically those made from Ti-6Al-4V, can have tensile strengths ranging from 130,000 to 160,000 psi (897 to 1103 MPa), depending on the specific heat treatment. The yield strength of this alloy can range from 120,000 to 140,000 psi (827 to 965 MPa). At first glance, these values might seem comparable or even slightly lower than Grade 8 bolts.
However, the strength-to-weight ratio is where titanium alloy bolts shine. Given that titanium is about 40% lighter than steel, a titanium bolt can provide similar strength to a Grade 8 bolt while weighing significantly less. This weight savings can be crucial in applications where every gram counts, such as in racing or aerospace.
Moreover, titanium's superior fatigue strength gives it an advantage in applications involving cyclic loading. Titanium alloys can withstand a higher number of stress cycles before failure compared to steel, which can translate to longer service life in certain high-stress, repetitive-load scenarios.
It's important to note that "strength" in the context of fasteners isn't solely about which material can withstand the highest absolute load. Factors such as elongation, ductility, and behavior under different types of stress (tensile, shear, fatigue) all play crucial roles in determining the overall performance and suitability of a fastener for a given application.
Corrosion Resistance and Biocompatibility
While not directly related to strength, corrosion resistance and biocompatibility are important properties that can influence the choice between titanium and Grade 8 bolts in certain applications.
Titanium alloys exhibit exceptional corrosion resistance due to their ability to form a stable, self-healing oxide layer on their surface. This property makes titanium bolts particularly suitable for use in harsh environments, such as marine applications or in the presence of corrosive chemicals. In contrast, while Grade 8 bolts can be treated for corrosion resistance (e.g., through zinc plating or other coatings), they generally do not match the inherent corrosion resistance of titanium.
Biocompatibility is another area where titanium excels. The human body tolerates titanium exceptionally well, with minimal risk of allergic reactions or rejection. This property, combined with its strength and corrosion resistance, makes titanium the material of choice for many medical implants, including bone screws and dental implants. While this might seem unrelated to automotive lug bolts, it demonstrates the versatility and unique properties of titanium that can be advantageous in specialized applications.
Grade 8 bolts, while strong and reliable, do not offer the same level of biocompatibility or corrosion resistance as titanium. However, for many standard automotive and industrial applications where these properties are not critical, Grade 8 bolts remain an excellent and cost-effective choice.
Titanium lug bolts manufacturer
When considering titanium lug bolts for high-performance applications, the choice of manufacturer is crucial to ensure quality and reliability. Wisdom Titanium stands out as a noteworthy option, particularly due to their ISO 9001 certification. This internationally recognized standard for quality management systems indicates that Wisdom Titanium has implemented and maintains robust processes to ensure consistent product quality and customer satisfaction.
ISO 9001 certification is particularly important for critical components like lug bolts, where product consistency and reliability are paramount. It suggests that the manufacturer adheres to strict quality control measures throughout their production process, from raw material selection to final product testing.
For those in the market for titanium lug bolts and evaluating potential manufacturers, reaching out to Wisdom Titanium at sales@wisdomtitanium.com could be a prudent step. Their ISO 9001 certification, combined with their specialization in titanium products, positions them as a promising option for high-quality, reliable titanium lug bolts.
In conclusion, while Grade 8 bolts may have higher absolute strength in some measures, titanium lug bolts offer a compelling combination of high strength, low weight, excellent fatigue resistance, and superior corrosion resistance. The choice between the two often depends on the specific application requirements, with titanium excelling in scenarios where weight savings, longevity in harsh environments, or biocompatibility are crucial. For standard automotive applications, Grade 8 bolts remain a strong, reliable, and cost-effective option. As with any critical component, the decision should be based on a thorough analysis of the specific application requirements and performance criteria.
References
- ASM International. Titanium: A Technical Guide. Materials Park, OH: ASM International.
- ASTM International. ASTM F467 - Standard Specification for Nonferrous Nuts for General Use. West Conshohocken, PA: ASTM International.
- Budynas, R. G., & Nisbett, J. K. Shigley's Mechanical Engineering Design. McGraw-Hill Education.
- International Organization for Standardization. Quality management systems — Requirements. Geneva
- Jain, R., & Lee, S. Fiber Metal Laminates: An Advanced Material for Future Aircraft Structures. Butterworth-Heinemann.
- National Highway Traffic Safety Administration. Tire and Wheel Safety. U.S. Department of Transportation.