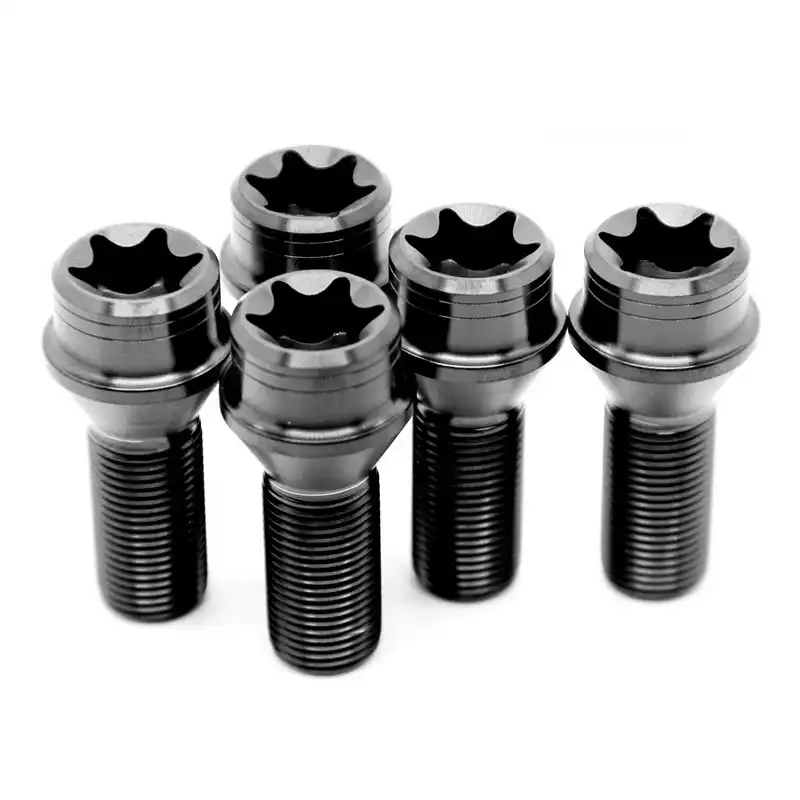
Introduction
Are titanium alloy wheel lug bolts safe? This question has been a topic of debate among automotive enthusiasts, performance drivers, and safety experts alike. As titanium lug bolts gain popularity in the automotive aftermarket, particularly in high-performance and racing applications, concerns about their safety and reliability have naturally arisen.
The controversy surrounding titanium lug bolts stems from several factors. On one hand, proponents argue that the superior strength-to-weight ratio of titanium alloys makes these bolts not just safe, but potentially safer than traditional steel bolts. They point to titanium's use in aerospace and other high-stress applications as evidence of its reliability. On the other hand, skeptics raise concerns about the different mechanical properties of titanium compared to steel, questioning whether these differences could lead to unexpected behavior under the extreme conditions experienced by wheel fasteners.
To address these concerns and provide a clear understanding of the safety of titanium lug bolts, we need to examine several key aspects: the material strength of titanium alloys, fatigue resistance, compliance with industry standards, and real-world applications in demanding environments.
Material strength
The strength of titanium alloys used in lug bolts is a crucial factor in assessing their safety. Typically, they are made from Ti-6Al-4V alloy, also known as Grade 5 titanium. This alloy is renowned for its excellent balance of strength, toughness, and corrosion resistance.
When comparing the strength of Ti-6Al-4V to common steel alloys used in lug bolts, the numbers are impressive. The ultimate tensile strength of Ti-6Al-4V ranges from 895 to 1125 MPa, depending on the heat treatment. This is comparable to, and in many cases exceeds, the strength of high-grade steel bolts. For example, Grade 8 steel bolts, commonly used in automotive applications, have a minimum tensile strength of 1034 MPa.
However, strength alone doesn't tell the whole story. Titanium alloys also have a lower modulus of elasticity compared to steel, meaning they can flex slightly more under load. While this property can be advantageous in some applications, providing better load distribution and resistance to fatigue, it also means that proper torque specifications are crucial when installing titanium lug bolts.
The yield strength of Ti-6Al-4V, typically around 828 MPa, is also noteworthy. This high yield strength means that they can withstand significant stress without permanent deformation, a critical factor in maintaining proper wheel attachment under varying loads.
Fatigue test
Fatigue resistance is perhaps even more critical than static strength when it comes to lug bolt safety. Wheel fasteners are subjected to cyclic loading and unloading with every rotation of the wheel, making fatigue failure a primary concern.
Titanium alloys, particularly Ti-6Al-4V, exhibit excellent fatigue resistance. In standardized fatigue tests, Ti-6Al-4V typically demonstrates a fatigue strength (at 10^7 cycles) of about 510 MPa. This means it can withstand cyclic loading at this stress level for 10 million cycles without failure. In comparison, many high-strength steels have fatigue strengths in the range of 200-400 MPa.
Practical fatigue testing of titanium lug bolts often involves simulating real-world conditions. For example, one study conducted by a major titanium fastener manufacturer subjected titanium lug bolts to a rotary beam fatigue test, simulating the alternating stresses experienced during vehicle operation. The results showed that properly manufactured titanium lug bolts could withstand over 10 million cycles at loads exceeding normal operating conditions without failure.
It's important to note that while these fatigue properties are impressive, they assume proper installation and maintenance. Over-torquing, under-torquing, or failure to re-torque after initial installation can significantly impact the fatigue life of any lug bolt, titanium or otherwise.
Industry standards
Titanium lug bolts, like their steel counterparts, must meet rigorous industry standards to be considered safe for automotive use. In the United States, these standards are primarily set by organizations such as the Society of Automotive Engineers (SAE) and the American Society for Testing and Materials (ASTM).
Key standards that apply to titanium lug bolts include:
1. SAE J429: While this standard primarily covers steel bolts, it sets benchmark mechanical properties that titanium bolts must meet or exceed.
2. ASTM F467: This standard specifically covers nonferrous nuts for general use, including those made from titanium alloys.
3. ISO 4014 and ISO 4017: These international standards cover hexagon head bolts, including specifications that titanium bolts must meet.
Reputable manufacturers of titanium lug bolts ensure their products meet or exceed these standards. Additionally, many undergo voluntary testing and certification processes to further validate their products' safety and performance.
It's worth noting that while meeting these standards is crucial, it's equally important for users to follow manufacturer guidelines for installation and use. Even the highest quality bolt can fail if improperly installed or used outside its design parameters.
Practical application
Perhaps the most compelling evidence for the safety of titanium lug bolts comes from their successful use in extremely demanding applications. In professional motorsports, where safety is paramount and components are pushed to their limits, they have become increasingly common.
Formula 1, often considered the pinnacle of motorsport technology, has used titanium wheel fasteners for years. These vehicles experience extreme forces during acceleration, braking, and cornering, yet titanium fasteners have proven reliable under these conditions.
In endurance racing, such as the 24 Hours of Le Mans, vehicles using titanium lug bolts have completed races covering thousands of kilometers at high speeds without wheel fastener failures. This real-world stress test provides strong evidence of the long-term reliability of properly engineered them.
Beyond racing, titanium fasteners have found use in aerospace applications, including critical components in commercial and military aircraft. The fact that titanium alloys are trusted in these high-stakes environments speaks volumes about their safety and reliability when properly engineered and installed.
Titanium lug bolts manufacturer
When considering the safety of titanium lug bolts, the choice of manufacturer is crucial. Wisdom Titanium stands out as a noteworthy option, particularly due to their ISO 9001 certification. This internationally recognized standard for quality management systems indicates that Wisdom Titanium has implemented and maintains robust processes to ensure consistent product quality and customer satisfaction.
ISO 9001 certification is particularly important for safety-critical components like lug bolts. It suggests that the manufacturer adheres to strict quality control measures throughout their production process, from raw material selection to final product testing. This systematic approach to quality management can significantly reduce the risk of defects or inconsistencies that could compromise safety.
For those in the market for titanium lug bolts and evaluating potential manufacturers, reaching out to Wisdom Titanium at sales@wisdomtitanium.com could be a prudent step. Their ISO 9001 certification, combined with their specialization in titanium products, positions them as a promising option for high-quality, reliable the products.
In conclusion, when properly manufactured, tested, and installed, titanium lug bolts can indeed be safe and reliable. Their high strength, excellent fatigue resistance, and successful use in demanding applications demonstrate their capability to perform safely under a wide range of conditions. However, as with any critical component, it's essential to purchase from reputable manufacturers, follow proper installation procedures, and adhere to recommended maintenance schedules to ensure ongoing safety and performance.
References
- ASM International. Titanium: A Technical Guide. Materials Park, OH: ASM International.
- ASTM International. ASTM F467 - Standard Specification for Nonferrous Nuts for General Use. West Conshohocken, PA: ASTM International.
- Budynas, R. G., & Nisbett, J. K. Shigley's Mechanical Engineering Design. McGraw-Hill Education.
- International Organization for Standardization. Quality management systems — Requirements. Geneva
- Jain, R., & Lee, S. Fiber Metal Laminates: An Advanced Material for Future Aircraft Structures. Butterworth-Heinemann.