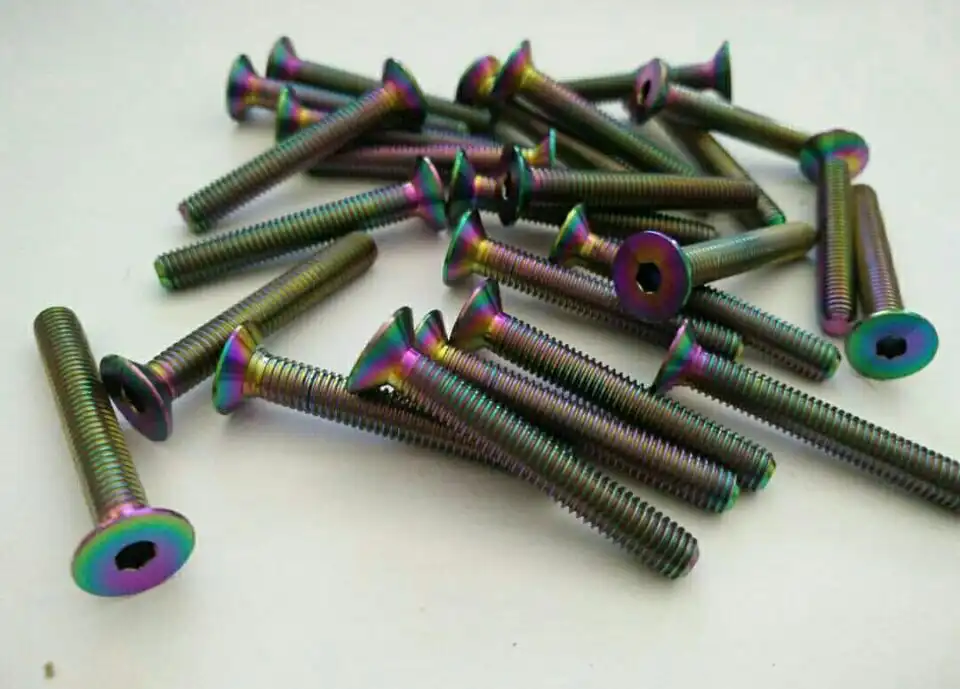
In my role as a fastener industry expert, inquiries about the suitability of titanium countersunk bolts with different materials are commonplace. Selecting the right fasteners is pivotal in construction and manufacturing endeavors, influencing the overall quality and durability of the end product significantly. This article delves into the topic of how titanium countersunk bolts interact with various materials, drawing on scientific research and practical insights to provide a comprehensive understanding of their compatibility. By examining the performance of titanium countersunk bolts in conjunction with different materials, we aim to offer valuable guidance to professionals seeking to make informed decisions when choosing fasteners for their projects.
In recent years, titanium countersunk bolts have experienced a surge in popularity attributable to their exceptional characteristics, such as a remarkable strength-to-weight ratio, resistance to corrosion, and biocompatibility. Widely embraced across diverse sectors like aerospace, automotive, marine, and medical industries, these bolts serve as critical components where dependability and longevity are of utmost importance. Their versatile applications extend to areas requiring steadfast performance and enduring quality, reflecting the trust placed in titanium countersunk bolts for mission-critical operations. Whether securing components in aircraft structures, enhancing automotive assemblies, fortifying marine vessels, or supporting medical devices, these bolts exemplify a commitment to excellence in engineering and innovation. The widespread adoption of titanium countersunk bolts underscores their pivotal role in advancing modern industry standards and underscores their status as indispensable elements in facilitating reliable and durable solutions across various sectors.
How crucial is material compatibility when utilizing titanium countersunk bolts in various industrial applications?
When utilizing titanium countersunk bolts, a key consideration revolves around their compatibility with a range of other materials, including steel, aluminum, and diverse composites. Compatibility denotes the capacity of two materials to effectively collaborate without inducing detrimental outcomes, such as galvanic corrosion, galling, or compromise of the joint's strength. This factor assumes paramount importance in various applications, spanning from aerospace and automotive engineering to marine and medical industries, where the seamless interaction between materials is essential for ensuring the reliability and longevity of assembled components. Adhering to stringent compatibility standards not only safeguards against potential material degradation but also underscores the meticulous approach required to achieve optimal performance and durability in complex assemblies. As such, the assessment and assurance of compatibility stand as critical considerations in the strategic selection and deployment of titanium countersunk bolts across diverse industrial domains.
Galvanic corrosion arises when disparate metals interact in the presence of an electrolyte, such as saltwater or moisture, initiating an electrochemical process that culminates in the degradation of the less noble metal. Titanium, renowned for its status as a noble metal and exceptional corrosion resistance across diverse settings, typically withstands environmental challenges adeptly. Nonetheless, when juxtaposed with less noble counterparts like steel or aluminum, the potential for galvanic corrosion emerges, posing a threat to the structural integrity of the connection. This phenomenon underscores the significance of material compatibility assessments in engineering applications, underscoring the need for strategic selection and pairing of metals to mitigate the risk of corrosion-induced deterioration. By recognizing the principles underpinning galvanic corrosion and proactively addressing material interactions, industries can uphold the durability and reliability of assemblies, ensuring optimal performance and longevity in varied operational environments.
In tackling this challenge, engineers frequently utilize strategies such as applying corrosion-resistant coatings to the bolts or incorporating insulating materials between dissimilar metals to forestall direct contact. Furthermore, meticulous attention to design and maintenance practices plays a pivotal role in mitigating the potential for galvanic corrosion within titanium bolt assemblies. These proactive measures serve to preemptively safeguard against the adverse effects of metal interactions, reinforcing the durability and reliability of the assembled components. By implementing these techniques, industries can effectively uphold the integrity of titanium bolt assemblies, ensuring sustained performance and longevity while minimizing the susceptibility to galvanic corrosion. This comprehensive approach underscores the importance of thoughtful engineering solutions and maintenance protocols in preserving the functionality and structural robustness of critical components across diverse industrial applications.
When employing titanium countersunk bolts, an additional factor to consider is their compatibility with various surface finishes. Titanium, characterized by a low coefficient of friction, has a propensity to gall when subjected to high pressure in contact with other metals. Galling represents a type of adhesive wear induced by the sliding or rubbing of two surfaces, resulting in material transfer and surface damage. This concern underscores the need for careful evaluation of surface finishes and lubrication methods to mitigate the risk of galling and ensure the integrity of the bolted joints. By addressing this aspect, industries can proactively manage potential challenges related to galling, emphasizing the importance of surface finish compatibility assessments and the implementation of suitable measures to uphold the performance and longevity of titanium countersunk bolt assemblies across diverse applications.
In order to alleviate the risk of galling, engineers often opt to administer lubricants or anti-seize compounds to the bolt threads prior to assembly. Furthermore, the selection of suitable surface finishes for mating components holds significance in diminishing the likelihood of galling and promoting seamless operation. By integrating these practices, industries can actively address the challenges associated with galling, emphasizing the proactive application of lubrication and the meticulous consideration of surface finish compatibility to uphold the operational efficiency and longevity of titanium countersunk bolt assemblies across diverse industrial contexts. These measures underscore the comprehensive approach required to manage the potential effects of galling, emphasizing the importance of thoughtful engineering solutions in securing the reliability and performance of critical components.
Beyond concerns of galvanic corrosion and galling, the mechanical characteristics of titanium countersunk bolts play a crucial role in assessing their compatibility with diverse materials. Renowned for its exceptional tensile strength and fatigue resistance, titanium proves well-suited for rigorous applications demanding robust performance. Nevertheless, its lower modulus of elasticity compared to steel presents a notable consideration, impacting the stiffness and deformation characteristics of the joint. This distinction underscores the necessity of evaluating how the mechanical properties of titanium interact with those of other materials to ensure optimal performance and structural integrity in assembled components. By acknowledging these factors, engineers can make informed decisions regarding material selection and design considerations, aiming to enhance the overall effectiveness and reliability of titanium countersunk bolt applications across a spectrum of demanding operational environments.
In the integration of titanium countersunk bolts with diverse materials, meticulous scrutiny of the mechanical attributes of each constituent is imperative to guarantee harmonious compatibility and structural soundness. Considerations encompassing load distribution, thermal expansion dynamics, and vibration characteristics assume paramount importance in preempting premature failure or distortion within the assembly. By delving into these critical facets, engineers can proactively avert potential setbacks, ensuring the seamless interaction and cohesive functionality of the assembled components. A comprehensive analysis of the mechanical properties serves as a linchpin in fostering durability and reliability, underscoring the necessity of a thorough assessment to mitigate risks and fortify the structural integrity of assemblies incorporating titanium countersunk bolts. Through this strategic approach, industries can navigate complexities effectively, fortifying the performance and longevity of assemblies across diverse operational contexts.
Conclusion
In summary, titanium countersunk bolts present a host of benefits including exceptional strength, corrosion resistance, and biocompatibility, making them highly advantageous for various applications. Nonetheless, their interaction with diverse materials necessitates meticulous analysis and engineering acumen to ascertain compatibility. Through a thorough grasp of potential challenges and the application of tailored mitigation approaches, engineers can adeptly integrate titanium fasteners into an array of scenarios with confidence. This strategic approach not only safeguards against potential pitfalls but also enhances the reliability and durability of assemblies incorporating titanium components. By proactively addressing compatibility issues and leveraging engineering expertise, industries can capitalize on the inherent advantages of titanium countersunk bolts, fostering optimal performance and longevity across a broad spectrum of applications.
If you want to learn more about Titanium Countersunk Bolts, welcome to contact us: sales@wisdomtitanium.com.
References
- J. R. Davis, "Handbook of Materials for Medical Devices," ASM International, 2003.
- D. L. Olson, "Handbook of Structural Engineering," CRC Press, 2005.
- A. H. Tuthill, "Fastener Design Manual," NASA, 1974.
- R. W. Hertzberg, "Deformation and Fracture Mechanics of Engineering Materials," Wiley, 1996.
- S. J. Zheng et al., "Galvanic Corrosion of Titanium Coupled to Dissimilar Metals in Artificial Saliva," Journal of Biomedical Materials Research Part B: Applied Biomaterials, vol. 105, no. 1, pp. 36-44, 2017.