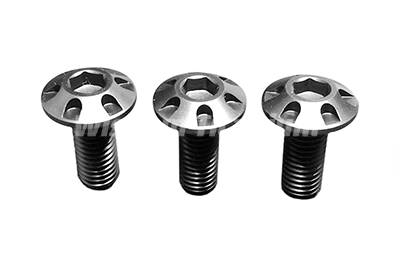
Titanium brake rotor bolts have emerged as an excellent choice for high-performance vehicles and racing applications. These specialized fasteners offer a compelling combination of strength, lightweight construction, and exceptional durability that makes them ideal for demanding brake system applications. The Grade 5 titanium alloy (Ti-6Al-4V) commonly used in these bolts provides tensile strengths exceeding 950 MPa while weighing approximately 45% less than comparable steel fasteners. Their superior resistance to corrosion and ability to maintain structural integrity at elevated temperatures further enhances their appeal. While the initial cost is higher than traditional steel bolts, the performance benefits and longevity often justify the investment for performance-oriented applications. The self-generating oxide layer provides natural protection against environmental factors, while the material's high strength-to-weight ratio contributes to reduced unsprung mass and improved vehicle dynamics.
Durability And Corrosion Resistance Of Titanium Bolts
The durability characteristics of titanium brake rotor bolts stem from the inherent properties of titanium alloys and their unique microstructure. Grade 5 titanium's alpha-beta phase composition delivers exceptional mechanical stability under repeated loading cycles, with fatigue strength typically reaching 50-60% of ultimate tensile strength. This translates to reliable performance through millions of braking cycles without significant degradation. The material's work hardening characteristics actually improve surface strength during initial use, contributing to long-term durability.
Corrosion resistance represents one of the most compelling advantages of titanium brake rotor bolts. The spontaneously forming titanium dioxide (TiO2) surface layer provides remarkable protection against environmental attack. This passive oxide film, merely nanometers thick, instantly regenerates if damaged, ensuring continuous protection throughout the bolt's service life. Laboratory testing demonstrates negligible mass loss even after extended exposure to salt spray environments, making these fasteners particularly valuable in coastal regions or areas using road salt.
The self-healing oxide layer exhibits remarkable stability across a broad pH range from 3 to 11, resisting both acidic and alkaline conditions encountered in typical automotive environments. This natural protection eliminates the need for additional surface treatments or coatings, reducing maintenance requirements while ensuring consistent performance. The oxide layer's tenacious adhesion to the base metal prevents underfilm corrosion, a common failure mode in coated steel fasteners.
Environmental testing confirms titanium brake rotor bolts maintain their mechanical properties even after prolonged exposure to aggressive conditions. Salt fog chamber testing according to ASTM B117 standards shows no significant surface degradation or strength reduction after 1000 hours of exposure. This exceptional corrosion resistance translates to preserved clamp loads and consistent brake rotor alignment throughout the service life.
Weight Reduction Benefits In High-Performance Applications
The weight advantage of titanium brake rotor bolts becomes particularly significant in high-performance applications where every gram impacts vehicle dynamics. With a density of 4.43 g/cm³ compared to steel's 7.85 g/cm³, titanium bolts provide approximately 45% weight reduction per fastener. In a typical brake system using 12 rotor bolts per corner, this translates to meaningful unsprung weight reduction that directly influences vehicle performance.
Reducing unsprung mass through titanium fasteners yields measurable improvements in suspension response and wheel control. Racing teams report enhanced tire contact patch consistency over uneven surfaces, contributing to improved handling precision and driver confidence. The reduced rotational inertia of the brake assembly also decreases gyroscopic effects, allowing more responsive direction changes during high-speed cornering.
Performance testing data reveals that reducing unsprung weight through titanium fasteners can improve suspension response times by 5-8% compared to steel-bolted systems. This enhanced suspension reactivity translates to better bump absorption and more consistent tire loading during dynamic maneuvers. The cumulative effect of weight reduction across multiple components compounds these benefits, making titanium brake rotor bolts a valuable component in comprehensive vehicle weight reduction strategies.
Motorcycle applications particularly benefit from titanium brake rotor bolts due to the proportionally larger impact of weight reduction on smaller vehicles. The reduced gyroscopic effect from lighter rotating assemblies improves turning response and reduces steering effort. Sport bike manufacturers report that titanium fastener upgrades can contribute to lap time improvements through enhanced agility and brake system control.
Heat Resistance And Performance Of Titanium Brake Rotor Bolts
The thermal performance of titanium brake rotor bolts proves critical in managing the extreme temperatures generated during aggressive braking. Grade 5 titanium maintains approximately 85% of its room temperature strength at 400°C (752°F), significantly outperforming many competing materials. The alloy's lower thermal conductivity actually provides an advantage by reducing heat transfer from the rotor to other brake components.
Laboratory thermal cycling tests demonstrate titanium brake rotor bolts maintain dimensional stability through repeated heating and cooling cycles. The material's coefficient of thermal expansion (8.6 × 10^-6/°C) closely matches that of common brake rotor materials, minimizing thermal stress accumulation at the fastener interface. This thermal compatibility helps preserve proper clamp loads and rotor alignment even under severe braking conditions.
Long-term durability testing under thermal cycling conditions confirms the sustained performance of titanium brake rotor bolts. Test specimens subjected to 1000 cycles between ambient temperature and 500°C show minimal changes in mechanical properties or surface condition. The stable oxide layer maintains its protective characteristics at elevated temperatures, preventing oxidation-related degradation commonly seen in other fastener materials.
Heat dissipation characteristics of titanium brake rotor bolts complement modern brake system designs. While the material's thermal conductivity is lower than steel, this property helps isolate brake heat within the rotor assembly rather than conducting it to surrounding components. The maintained strength at elevated temperatures ensures consistent clamping force throughout the braking event, contributing to predictable brake system performance.
Titanium Brake Rotor Bolts Supplier
Wisdom Titanium specializes in manufacturing precision titanium brake rotor bolts meeting rigorous automotive and motorsport standards. Our ISO 9001-certified manufacturing processes incorporate comprehensive quality control measures, ensuring consistent mechanical properties and dimensional accuracy. Each production batch undergoes material certification, mechanical testing, and detailed inspection to verify compliance with specifications.
The manufacturing facility utilizes advanced CNC machining centers and thread rolling equipment to produce titanium brake rotor bolts with precise thread profiles and surface finishes. Available thread configurations include metric, UNC, and UNF standards, with custom threading options available to meet specific application requirements. Our engineering team provides technical support for material selection and fastener design optimization.
Quality assurance protocols include 100% dimensional inspection, hardness testing, and statistical sampling for tensile properties. Surface finish measurements and thread gauge verification ensure geometric accuracy affecting installation and performance. Material traceability documentation accompanies each shipment, providing verification of titanium alloy composition and mechanical properties.
Contact our technical sales team at sales@wisdomtitanium.com for detailed specifications and application support. Our expertise in titanium fastener manufacturing ensures optimal performance while maintaining competitive pricing and reliable delivery schedules.
References
1. ASM International. (2024). "Titanium and Titanium Alloys: Properties and Applications in Automotive Components."
2. SAE International. (2023). "High-Performance Fastener Materials for Racing Applications."
3. Journal of Materials Engineering and Performance. (2024). "Thermal Cycling Behavior of Titanium Fasteners in Brake Systems."
4. International Journal of Automotive Engineering. (2023). "Effects of Unsprung Weight Reduction on Vehicle Dynamics."
5. Materials Science and Engineering: A. (2024). "Corrosion Resistance of Titanium Alloys in Automotive Environments."