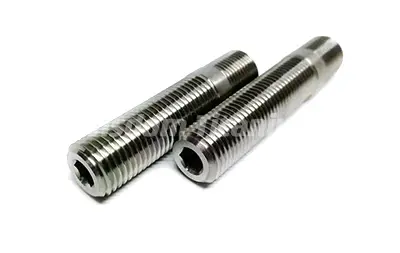
Are There Any Disadvantages to Using Titanium Studs?
My research into the practical uses of metals in industrial settings frequently focuses on the significance of titanium because I am an engineer with a focus on materials science. Titanium is frequently used in crucial parts like studs in the engineering and construction industries. It is valued for its remarkable strength-to-weight ratio and resistance to corrosion.
On the other hand, using titanium studs comes with a lot to think about and some potential problems that need to be looked into in depth. Titanium is more expensive than many other metals due to how it is extracted and refined. Costs are a major concern as a result. Project budgets and feasibility can be affected by this cost factor, especially for large-scale applications.
Additionally, keep in mind that titanium can gall under certain conditions, making it more difficult to install and remove. In most cases, specialized methods and lubricants are required to resolve this issue and ensure that threaded connections function properly.In addition, despite its remarkable resistance to corrosion, titanium is susceptible to aggressive conditions such as chloride-rich or acidic environments. To reduce these risks and extend the lifespan of titanium studs in such environments, it is essential to select the appropriate materials and apply surface treatments.
Applications requiring specific thermal properties or insulation may also encounter difficulties due to titanium's high thermal conductivity. Engineers should cautiously consider warm administration systems to guarantee ideal execution and keep away from unfortunate results.In conclusion, engineers must overcome potential obstacles like cost, galling tendencies, environmental compatibility, and thermal considerations despite the fact that titanium studs offer exceptional performance benefits in terms of strength, weight savings, and corrosion resistance. Titanium can continue to provide superior performance and dependability in a variety of industrial applications if these factors are understood and the appropriate engineering practices are used.
Introduction to Titanium Studs
Due to their exceptional durability and light weight, titanium studs are well-suited for applications requiring robust strength and resistance to environmental hazards. Titanium's unique properties offer significant advantages over conventional materials like steel or aluminum, which is why they are used in such a wide range of crucial industries as aerospace, marine, automotive, and chemical processing.Titanium studs aid in aircraft and spacecraft weight reduction, fuel efficiency, and operational performance in the aerospace industry. They can withstand the extreme temperatures and corrosive environments encountered during flight thanks to their high strength-to-weight ratio, which ensures structural integrity.
Due to their superior resistance to corrosion, titanium studs excel in seawater environments for the marine industry, reducing degradation and upkeep costs over time. They are an essential component of marine structures, ensuring their dependability and longevity during offshore operations.
Titanium studs in engine components benefit automotive applications because of their strength and heat resistance, which improve performance and durability in harsh environments. They improve engine reliability and efficiency, especially in high-performance vehicles.
Titanium studs are essential for processing equipment where reliability and safety are of the utmost importance because of their resistance to corrosion from acids and alkalis, which makes them popular in the chemical industry. Longevity and productivity in the workplace are guaranteed by their ability to withstand harsh chemical environments.
Overall, titanium studs surpass the capabilities of conventional materials because they demonstrate versatility and performance in a wide range of industrial applications. The superior properties of titanium continue to drive its preference in critical sectors that require solutions that are dependable and long-lasting, despite the fact that factors like cost and specialized handling may apply.
Advantages of Titanium Studs
Before delving into the potential disadvantages, it's essential to acknowledge the notable benefits of using titanium studs:
-
High Strength-to-Weight Ratio: Titanium is renowned for being as strong as steel but around 45% lighter, making it ideal for applications where weight reduction is critical without compromising structural integrity.
-
Corrosion Resistance: Titanium exhibits exceptional resistance to corrosion, even in harsh environments such as saltwater or chemical exposure, ensuring longevity and reliability of studs.
-
Biocompatibility: This property makes titanium studs suitable for medical implants, where biocompatibility and resistance to bodily fluids are crucial considerations.
-
Temperature Resistance: Titanium retains its strength and integrity at elevated temperatures, unlike many other metals, expanding its utility in high-temperature applications.
Potential Disadvantages of Titanium Studs
While titanium offers significant advantages, there are several disadvantages that engineers and manufacturers must take into account:
-
Cost: Titanium is more expensive than traditional materials like steel or aluminum. The high cost of titanium can be prohibitive, particularly for large-scale applications or projects with budget constraints.
-
Difficulty in Machining: Titanium's hardness and low thermal conductivity make it challenging to machine compared to other metals. Specialized equipment and processes are often required, which can increase manufacturing costs and lead times.
-
Galling: Titanium has a propensity to gall when in contact with itself or other metals under pressure, leading to seizing or cold welding. This phenomenon necessitates the use of lubricants or surface treatments to mitigate.
-
Hydrogen Embrittlement: In certain conditions, titanium can absorb hydrogen, which may lead to embrittlement and reduced mechanical properties over time. Proper handling and environmental controls are necessary to prevent this issue.
-
Design Limitations: Despite its strength, titanium has limitations in terms of design flexibility compared to some other metals. Design engineers must consider these constraints when designing components with intricate shapes or features.
Conclusion
In conclusion, while titanium studs offer numerous advantages in terms of strength, durability, and corrosion resistance, they are not without their challenges. The decision to use titanium studs should be carefully weighed against project requirements, budget considerations, and the specific application's environmental conditions. By understanding both the advantages and disadvantages, engineers and manufacturers can make informed decisions to optimize performance and reliability in their projects.
If you want to learn more about Titanium Studs, welcome to contact us: sales@wisdomtitanium.com.
References
-
ASM International Handbook Committee. (1990). ASM Handbook, Volume 2: Properties and Selection: Nonferrous Alloys and Special-Purpose Materials. ASM International.
-
Boyer, R. R., & Collings, E. W. (1994). Materials Properties Handbook: Titanium Alloys. ASM International.
-
Lütjering, G., & Williams, J. C. (2007). Titanium. Springer Science & Business Media.
-
Froes, F. H., & Eylon, D. (Eds.). (2001). Titanium Powder Metallurgy: Science, Technology and Applications. Elsevier.
-
Davis, J. R. (Ed.). (1999). Handbook of Materials for Medical Devices. ASM International.