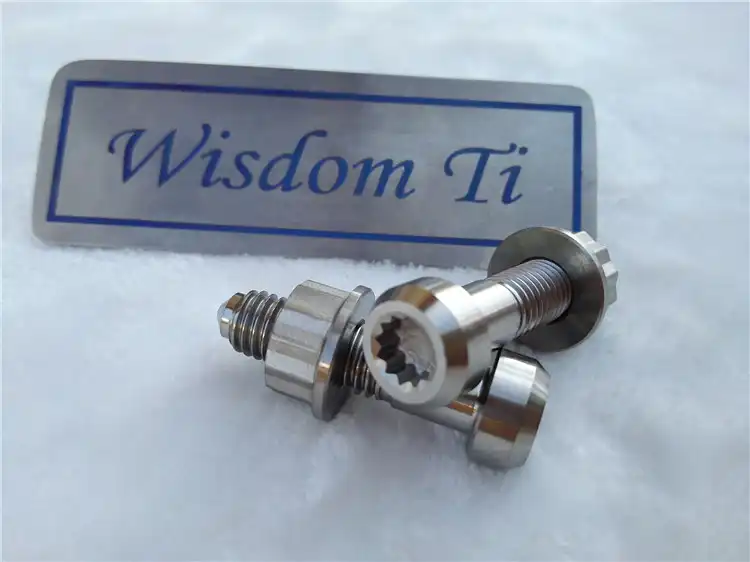
Titanium alloys have long been admired in the materials science and engineering community for their exceptional properties, and custom titanium rim bolts exemplify their remarkable capabilities.These particular clasp assume a basic part in different businesses, including auto, aviation, and athletic gear, where lightweight, high-strength, and consumption safe parts are fundamental.
One of the key attributes that make custom titanium rim bolts highly sought after is their outstanding corrosion resistance. Unlike many other metals, titanium alloys possess a natural oxide layer that forms on their surface, providing inherent protection against corrosion in various environments, including exposure to moisture, saltwater, and chemicals. This oxide layer acts as a barrier, preventing further oxidation and degradation of the material, thereby enhancing the longevity and reliability of the rim bolts.
Moreover, the corrosion resistance of custom titanium rim bolts can be further enhanced through advanced surface treatments and coatings. Procedures, for example, anodizing, electroplating, and PVD (Actual Fume Affidavit) covering can be utilized to adjust the surface properties of titanium amalgams, working on their protection from explicit destructive specialists and natural circumstances.These surface treatments not only enhance the aesthetic appeal of the rim bolts but also contribute to their overall performance and durability.
Can Custom Titanium Rim Bolts Resist Corrosion?
Understanding the corrosion mechanisms of titanium alloys is crucial for evaluating the corrosion resistance of custom titanium rim bolts. Titanium is prestigious for its excellent solidarity to-weight proportion and biocompatibility, credits that contribute essentially to its erosion opposition through the development of a defensive oxide layer on its surface. This oxide layer, principally made out of titanium dioxide (TiO2), goes about as a hindrance against ecological components like dampness, oxygen, and destructive substances.
However, it's important to acknowledge that titanium alloys can still corrode under specific conditions, especially in aggressive environments like marine or chemical processing settings. Various factors influence the corrosion behavior of titanium alloys, including alloy composition, surface finish, temperature, pH levels, and exposure to corrosive agents.
Therefore, ensuring the corrosion resistance of custom titanium rim bolts requires meticulous alloy selection and manufacturing processes tailored to enhance their protective properties. By optimizing alloy compositions, surface treatments, and manufacturing techniques, it's possible to improve the corrosion resistance of titanium alloys, thus ensuring the reliability of custom titanium rim bolts in diverse environmental conditions.
How to Assess Corrosion Resistance in Titanium Rim Bolts?
When assessing the corrosion resistance of custom titanium rim bolts, several key factors come into play. Firstly, the alloy composition plays a pivotal role, with specific alloying elements added to enhance corrosion resistance. Common alloying elements include aluminum, vanadium, and nickel, each contributing to the formation of a more robust and stable oxide layer.
Furthermore, the surface finish of custom titanium rim bolts significantly influences their corrosion resistance. Smooth, polished surfaces facilitate the formation of a uniform oxide layer, whereas rough or contaminated surfaces may compromise the protective barrier, rendering the bolts more susceptible to corrosion. Therefore, meticulous surface treatment processes, such as passivation or anodizing, are often employed to optimize the corrosion resistance of custom titanium rim bolts.
Additionally, environmental factors must be considered when evaluating the corrosion resistance of titanium rim bolts. Exposure to corrosive substances, varying pH levels, temperature fluctuations, and mechanical stresses can all impact the performance of these fasteners over time. Hence, thorough testing under simulated operating conditions is imperative to ensure the reliability and longevity of custom titanium rim bolts in real-world applications.
Are Custom Titanium Rim Bolts Corrosion-Tested?
In the pursuit of excellence and reliability, the manufacturing and testing of custom titanium rim bolts adhere to stringent industry standards and protocols. Associations like ASTM Worldwide and the Global Association for Normalization (ISO) lay out rules and particulars for the manufacture and portrayal of titanium compounds, including consumption testing systems.
Standardized corrosion tests, such as salt spray testing (ASTM B117) and electrochemical impedance spectroscopy (EIS), provide valuable insights into the corrosion resistance of custom titanium rim bolts under controlled laboratory conditions. These tests simulate harsh environmental conditions and assess the performance of titanium alloys in resisting corrosion over extended periods.
Furthermore, quality assurance measures, including material certification and traceability, ensure that custom titanium rim bolts meet the highest standards of excellence and reliability. By adhering to industry best practices and continuously refining manufacturing processes, manufacturers uphold the integrity and performance of these critical components in diverse applications.
Conclusion
In conclusion, the corrosion resistance of custom titanium rim bolts is a multifaceted aspect that necessitates a holistic understanding of materials science, engineering principles, and environmental factors. Through meticulous alloy selection, surface treatment, and adherence to industry standards, manufacturers strive to deliver titanium fasteners of unparalleled quality and durability. While challenges may arise in harsh operating environments, the inherent corrosion resistance of titanium alloys, coupled with advanced manufacturing techniques, instills confidence in the reliability and longevity of custom titanium rim bolts.
If you want to know more about Customized Titanium Rim Bolts, please contact us: sales@wisdomtitanium.com.
References:
- ASM Handbook Volume 13A: Corrosion: Fundamentals, Testing, and Protection
- ASTM B117 - Standard Practice for Operating Salt Spray (Fog) Apparatus
- International Organization for Standardization (ISO) 5832-2:2018 - Implants for surgery — Metallic materials — Part 2: Unalloyed titanium