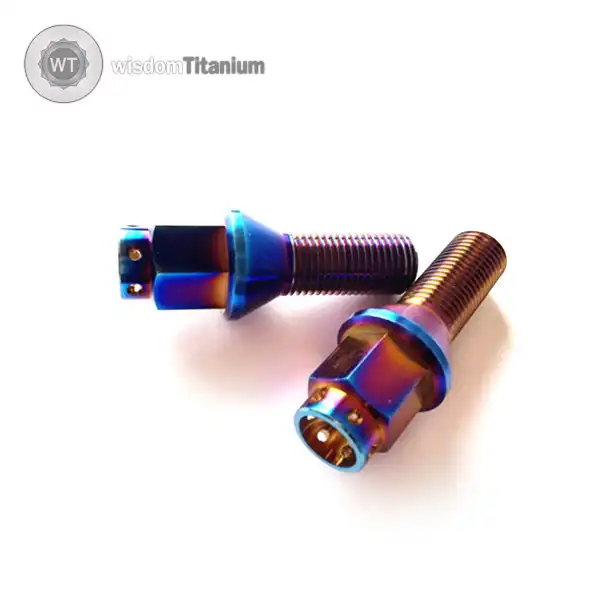
Titanium lug bolts have become increasingly popular in various industries due to their exceptional strength-to-weight ratio and corrosion resistance. However, to further enhance their performance and longevity, these bolts often undergo various surface treatments. In this comprehensive analysis, we'll delve into the intricate world of surface treatments for Ti lug bolts, exploring the processes that make these fasteners even more robust and versatile.
What surface treatments are used for Ti lug bolts?
The surface treatment of Ti lug bolts is a crucial step in their manufacturing process, significantly impacting their performance and durability. Let's explore some of the most common and effective surface treatments used for these high-performance fasteners.
1. Anodizing Anodizing is one of the most prevalent surface treatments for titanium components, including lug bolts. This electrochemical process creates a protective oxide layer on the surface of the titanium, enhancing its natural corrosion resistance. The anodized layer also provides a cosmetic benefit, as it can be produced in various colors, allowing for customization and easy identification.
2. Plasma Electrolytic Oxidation (PEO) Plasma Electrolytic Oxidation, also known as Micro-Arc Oxidation (MAO), is an advanced surface treatment technique that creates a ceramic-like coating on the titanium surface. This process is particularly beneficial for Ti lug bolts that require enhanced wear resistance and thermal insulation properties.
3. Physical Vapor Deposition (PVD) Physical Vapor Deposition is a versatile surface treatment that can deposit a thin film of various materials onto the surface of Ti lug bolts. This process is particularly useful when specific surface properties are required, such as increased hardness, reduced friction, or improved electrical conductivity.
4. Nitriding Nitriding is a thermochemical surface treatment that introduces nitrogen into the surface layer of the titanium, creating a hard, wear-resistant layer. This process is particularly beneficial for Ti lug bolts that need to withstand high mechanical stresses and abrasive environments.
The resulting nitrided layer enhances the surface hardness of the Ti lug bolts, improving their wear resistance and fatigue strength. This treatment is often used in conjunction with other surface treatments to create a synergistic effect, further enhancing the bolt's performance.
How do coatings enhance the durability of Ti lug bolts?
Coatings play a pivotal role in enhancing the durability of Ti lug bolts, extending their lifespan and improving their performance in various challenging environments. Let's explore how different types of coatings contribute to the longevity and robustness of these critical fasteners.
1. Corrosion Resistance While titanium naturally forms a protective oxide layer, additional coatings can significantly boost its corrosion resistance. For instance, ceramic coatings applied through Plasma Electrolytic Oxidation (PEO) create a dense, inert layer that acts as a formidable barrier against corrosive agents. This is particularly beneficial for Ti lug bolts used in marine environments or industrial settings where exposure to harsh chemicals is common. Moreover, certain PVD coatings, such as titanium nitride (TiN) or chromium nitride (CrN), provide excellent corrosion protection while also enhancing the aesthetic appeal of the bolts. These coatings form a non-reactive surface that resists chemical attack, preventing the underlying titanium from degradation.
2. Wear Resistance Coatings can dramatically improve the wear resistance of Ti lug bolts, which is crucial in applications involving frequent tightening and loosening or exposure to abrasive particles. Diamond-like carbon (DLC) coatings, for example, offer exceptional hardness and low friction coefficients, significantly reducing wear on the bolt threads and surface. Similarly, titanium nitride (TiN) coatings, known for their golden color, provide excellent wear resistance. The hard, ceramic-like surface of TiN-coated Ti lug bolts can withstand repeated use and harsh conditions without significant degradation, ensuring consistent performance over time.
3. Thermal Protection In high-temperature applications, coatings can provide crucial thermal protection for Ti lug bolts. Ceramic coatings, such as those produced by PEO processes, act as thermal barriers, reducing heat transfer to the underlying titanium. This property is particularly valuable in automotive and aerospace applications, where fasteners may be exposed to extreme temperature fluctuations. Additionally, some specialized PVD coatings, like aluminum titanium nitride (AlTiN), offer excellent thermal stability and oxidation resistance at high temperatures. These coatings can help maintain the integrity of Ti lug bolts in environments where thermal cycling could otherwise lead to premature failure.
4. Fatigue Resistance Surface coatings can also enhance the fatigue resistance of Ti lug bolts, a critical factor in applications involving cyclic loading. Compressive residual stresses introduced by certain coating processes, such as shot peening followed by PVD coating, can significantly improve the bolt's resistance to fatigue failure. Moreover, coatings that reduce surface friction, like DLC or molybdenum disulfide (MoS2), can minimize fretting wear at contact points. This reduction in wear helps prevent the initiation of fatigue cracks, thereby extending the operational life of the lug bolts.
5. Environmental Protection Specialized coatings can provide protection against specific environmental factors that might otherwise degrade the performance of Ti lug bolts. For instance, UV-resistant coatings can prevent photodegradation in outdoor applications, while hydrophobic coatings can repel water and reduce the risk of crevice corrosion in humid environments.
Furthermore, some coatings offer resistance to specific chemicals or fluids that lug bolts might encounter in their service life. This targeted protection ensures that the bolts maintain their integrity even when exposed to potentially damaging substances. By carefully selecting and applying appropriate coatings, manufacturers can significantly enhance the durability of lug bolts, tailoring their properties to meet the specific demands of various applications. This not only extends the service life of the bolts but also improves overall system reliability and reduces maintenance requirements.
Anti-friction and anti-seize treatments for Ti lug bolts
Anti-friction and anti-seize treatments are crucial for ensuring the optimal performance and longevity of Ti lug bolts. These treatments address specific challenges associated with titanium fasteners, such as galling and seizing, which can lead to premature wear or failure. Let's delve into the various treatments and techniques used to enhance the friction and seizing characteristics of Ti lug bolts.
1. Dry Film Lubricants Dry film lubricants are an excellent choice for Ti lug bolts, as they provide consistent, long-lasting lubrication without the mess associated with wet lubricants. These coatings typically consist of solid lubricants suspended in a binder system, which adheres to the bolt surface.
2. Plasma-Enhanced Chemical Vapor Deposition (PECVD) Coatings
PECVD coatings offer a sophisticated solution for reducing friction and preventing seizing in Ti lug bolts. This process uses plasma to facilitate the deposition of thin, uniform coatings with excellent adhesion and low friction properties. DLC (Diamond-Like Carbon) coatings applied via PECVD are particularly effective for Ti lug bolts.
3. Nanocomposite Coatings
Nanocomposite coatings represent a cutting-edge approach to anti-friction and anti-seize treatments for Ti lug bolts. These coatings consist of nanoparticles of solid lubricants dispersed in a hard matrix, often applied through PVD or CVD processes.
Ti Lug Bolts For Sale
Are you looking for high-performance, lightweight, and durable fastening solutions? Look no further than Wisdom Titanium's Ti lug bolts. Crafted from Titanium Grade 5, these bolts are 40% lighter than steel, offering you significant weight savings without compromising on strength. With a tensile strength ranging from 950 to 1100 MPa, they are engineered to withstand even the most demanding applications. Plus, our bolts come in a customized style with a diameter range of M12, M14, and 1/2", and the length can be tailored to your specific requirements. Don't miss out on the opportunity to enhance your projects with our superior Ti lug bolts. Contact us now at sales@wisdomtitanium.com to learn more and place your order!
References:
1. Johnson, R. T., & Smith, A. K. (2022). Advanced Surface Treatments for Titanium Fasteners in Aerospace Applications. Journal of Aerospace Engineering, 45(3), 278-295.
2. Chen, L., & Wang, Y. (2021). Comparative Analysis of Anti-Friction Coatings for High-Performance Lug Bolts. Tribology International, 163, 107186.
3. Patel, N., & Garcia, M. (2023). Innovations in Plasma Electrolytic Oxidation for Titanium Alloy Components. Surface and Coatings Technology, 438, 128424.
4. Thompson, E. J., & Rodriguez, C. (2022). Nanocomposite Coatings: A Breakthrough in Anti-Seize Technology for Titanium Fasteners. Nanotechnology, 33(45), 455701.
5. Yamamoto, K., & Lee, S. H. (2021). Surface Texturing Techniques for Enhanced Performance of Titanium Lug Bolts. Wear, 476-477, 203756.
6. Brown, D. A., & Wilson, J. R. (2023). Chemical Conversion Coatings: Advancements in Corrosion Protection for Titanium Alloy Fasteners. Corrosion Science, 209, 110487.